our process
American Elkhart Manufacturing staff are capable of consulting with clients during the design phase,offering assistance in conceptualizing rubber and plastic solutions.
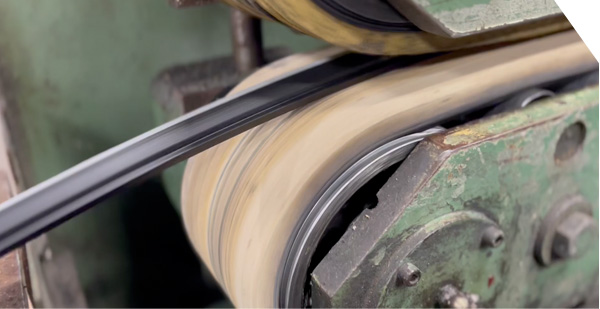
DESIGN ASSISTANCE
American Elkhart Manufacturing staff are capable of consulting with clients during the design phase,offering assistance in conceptualizing rubber and plastic solutions.
Alongside your engineering team, we’ll assess the project needs, collaborate in structuring a working design and implement it among our production line. Though we propose direction in designing, American Elkhart Manufacturing is not design-responsible for projects.
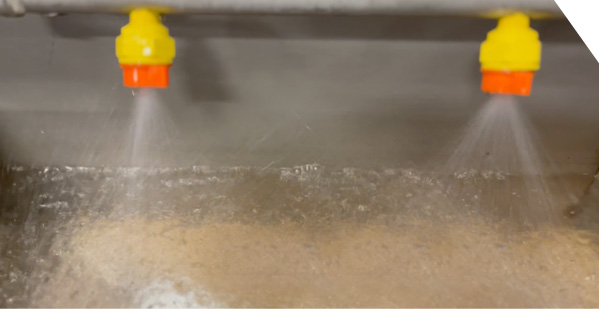
MATERIAL SELECTION
We work together with our clients, applying our experience and knowledge to determine the best material for application. Often, our clients have a particular material in mind; if they do not, we can offer direction in selecting a material suitable for certain temperatures or other environmental demands.
EXTRUSION PROCESS
Our plastic extrusion manufacturing process creates ongoing, uniform, two-dimensional, cross-sectional consistency with a range of materials and specifications. This process includes:
- Thermoplastic raw material comes in pre-compounded pellet form.
- Plastic raw material arrives in pellet form.
- Heat within the extruder softens the plastic as it is pushed through the die tool opening.
- The die opening shapes the plastic into a finished part.
- The plastic is cooled as it moves downstream, where it is ultimately cut or spooled for shipment.
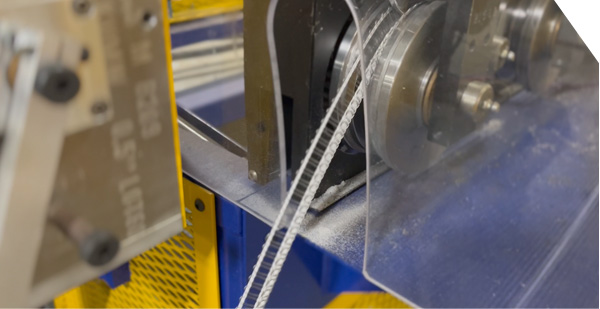
SECONDARY OPERATIONS
We work together with our clients, applying our experience and knowledge to determine the best material for application. Often, our clients have a particular material in mind; if they do not, we can offer direction in selecting a material suitable for certain temperatures or other environmental demands.
Though extrusion is our speciality, American Elkhart Manufacturing staff are also capable of:
- Drilling & Patching
- Inline Printing
- Notching
- Special & Private
- Taping (HATS & PSA)
- Cutting