Neoprene vs. EPDM Seals: A Comprehensive Comparison for Diverse Industries
Seals play a vital role in various industries, ensuring critical components remain protected
and leak-free. Two commonly used types of seals are neoprene and EPDM (Ethylene Propylene Diene Monomer) seals, both of which are synthetic rubbers available from American Elkhart, along with molded or extruded plastic seals that can serve as a more cost-effective alternative.
In this blog post, we’ll explore the differences between neoprene and EPDM rubber seals, specifically in the context of extrusion and their applications in final form, as types of seals we offer. Additionally, we'll discuss which industries benefit from each of these versatile sealing materials.
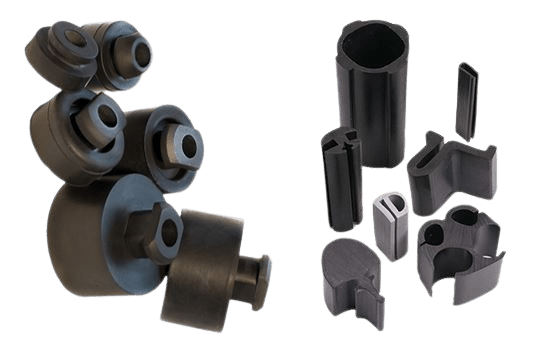
EPDM Seals
EPDM seals are another synthetic rubber compound, characterized by their outstanding weather and ozone resistance while offering distinct advantages for various scenarios:
Weather Resistance
EPDM seals excel in outdoor applications due to their exceptional resistance to ozone and UV exposure. This makes them suitable for applications exposed to the elements, like roofing or automotive weatherstripping.
Chemical Resistance
EPDM seals are compatible with a broad range of chemicals, which is an advantage in industries where exposure to diverse fluids is common.
Temperature Tolerance
EPDM seals can endure high and low temperatures, making them ideal for applications subject to extreme weather conditions.
Water & Steam Resistance
EPDM seals have excellent water and steam resistance, making them a preferred choice in industries requiring protection against moisture and high humidity.
Longevity
EPDM seals have a long service life and are less susceptible to wear and tear, resulting in reduced maintenance costs.
Let’s look at some of the various EPDM seals available through American Elkhart.
Single Durometer EPDM
Single durometer EPDM seals are made from a single material hardness, meaning the entire seal has consistent hardness and flexibility throughout.
Weather Sealing
These seals are used in manufacturing environments for weatherstripping, gaskets and seals that need to protect against moisture, UV radiation and extreme temperatures.
Vibration Dampening
Single durometer EPDM seals are also effective for vibration isolation in machinery or equipment to prevent noise and protect sensitive components.
Dual Durometer EPDM Seals
Dual durometer EPDM seals combine two different materials with varying hardness within a single seal. Typically, a harder EPDM is used as a backbone, with a softer EPDM as the sealing face.
Enclosures and Cabinets
Dual durometer seals are suitable for enclosures and cabinets to provide a durable seal that resists environmental conditions while maintaining a soft contact surface to ensure an airtight or watertight seal.
Equipment Access Panels
They can be used on access panels of machinery or equipment to allow easy access while maintaining a secure seal when closed.
Taped EPDM Seals
Taped EPDM seals involve the application of an adhesive (tape) to one side of the EPDM material. This adhesive backing simplifies installation and ensures a secure attachment to surfaces.
Manufacturing Joints
Taped EPDM seals are commonly used in manufacturing environments to seal joints and seams in equipment or structures, providing protection against dust, moisture and environmental factors.
Door and Window Sealing
They can be used to seal doors, windows and hatches in manufacturing facilities to maintain a controlled environment.
Clip-On EPDM Seals
Clip-on EPDM seals are designed with a profile that allows them to be easily attached or clipped onto the edges of panels, doors or other surfaces.
Access Panels
Clip-on seals are used to seal access panels and doors on machinery and equipment. They provide a quick and secure way to maintain a tight seal.
Containment Systems
These seals are applied to containment systems, such as cleanrooms and manufacturing areas that require a dust-free or controlled environment, ensuring a tight seal at connecting points.
Industries Typically Employing EPDM Seals
Construction and Roofing Industry
EPDM seals are prevalent in roofing materials, providing a durable and weather-resistant solution for waterproofing and weatherstripping applications.
Automotive Weatherstripping
EPDM seals are used extensively in automotive applications, especially for weatherstripping and sealing against the elements.
Chemical Processing
Industries dealing with a wide range of chemicals, like the chemical processing sector, employ EPDM seals for their chemical compatibility and durability.
HVAC and Refrigeration
EPDM seals are used in HVAC systems and refrigeration equipment to maintain effective seals and withstand temperature variations.
Outdoor and Recreational Equipment
Industries producing outdoor and recreational equipment, such as boats, RVs, and playground equipment, rely on EPDM seals for their weather-resistant properties.
Neoprene Seals
Neoprene seals are another synthetic rubber compound known for their resilience and versatility. These seals offer several characteristics that make them suitable for various industries.
Temperature Resistance
Neoprene seals are renowned for their ability to withstand a wide range of temperatures. This makes them an excellent choice for applications where temperature fluctuations are common, such as in automotive or industrial settings.
Flexibility
Neoprene is highly flexible, allowing it to conform to irregular shapes and surfaces. This flexibility is a significant advantage in applications where sealing materials need to adapt to varying contours.
Chemical Resistance
Neoprene has good resistance to many chemicals, making it a viable choice for applications that involve contact with different fluids, such as gasoline.
Durability
Neoprene seals are durable and offer a relatively long service life, which can lead to reduced maintenance costs over time.
Cost-Effectiveness
Neoprene is cost-effective, making it a popular choice in industries with budget constraints.
However, neoprene seals have some limitations, including reduced resistance to ozone and ultraviolet (UV) exposure. Additionally, they may not perform well in the presence of certain chemicals and oils.
Industries Benefitting from Neoprene Seals
Automotive
Neoprene seals are widely used in automotive applications, including engine gaskets, door and window seals and suspension components due to their temperature resistance and flexibility.
Manufacturing
Neoprene seals are employed in various manufacturing applications to prevent leaks and ensure the efficiency of machinery and extrusion processes.
Construction
Neoprene seals are used in the construction sector to seal windows, doors and concrete expansion joints, where flexibility is essential.
Marine and Offshore
Due to their resistance to saltwater and UV exposure, neoprene seals are used in boat and shipbuilding, as well as for sealing offshore structures and equipment.
Agricultural and Heavy Equipment
Neoprene seals can protect sensitive electronic components and are used in hydraulic systems, where they must withstand pressure and temperature variations.
How American Elkhart Can Help
The choice between neoprene and EPDM seals in any application depends on the specific requirements and environmental conditions of the industry. Neoprene is often ideal for applications requiring flexibility, cost-effectiveness and resistance to temperature fluctuations. In contrast, EPDM seals excel in outdoor and chemical-heavy applications, providing superior weather resistance, chemical compatibility and durability.
In some cases, American Elkhart’s extruded or molded plastic products can be a more desirable alternative to EPDM or neoprene rubber seals as they are similar in effectiveness without a required curing process, which can drive manufacturing costs higher. Making an informed choice between these seal types will ensure the efficiency and reliability of your industry's operations.
Have a question about which material may be best for your needs? Would you like to learn more about American Elkhart’s extrusion and molding capabilities?
Contact us today, and one of staff members can assist in answering any questions while guiding you to a suitable solution!
Recent Posts
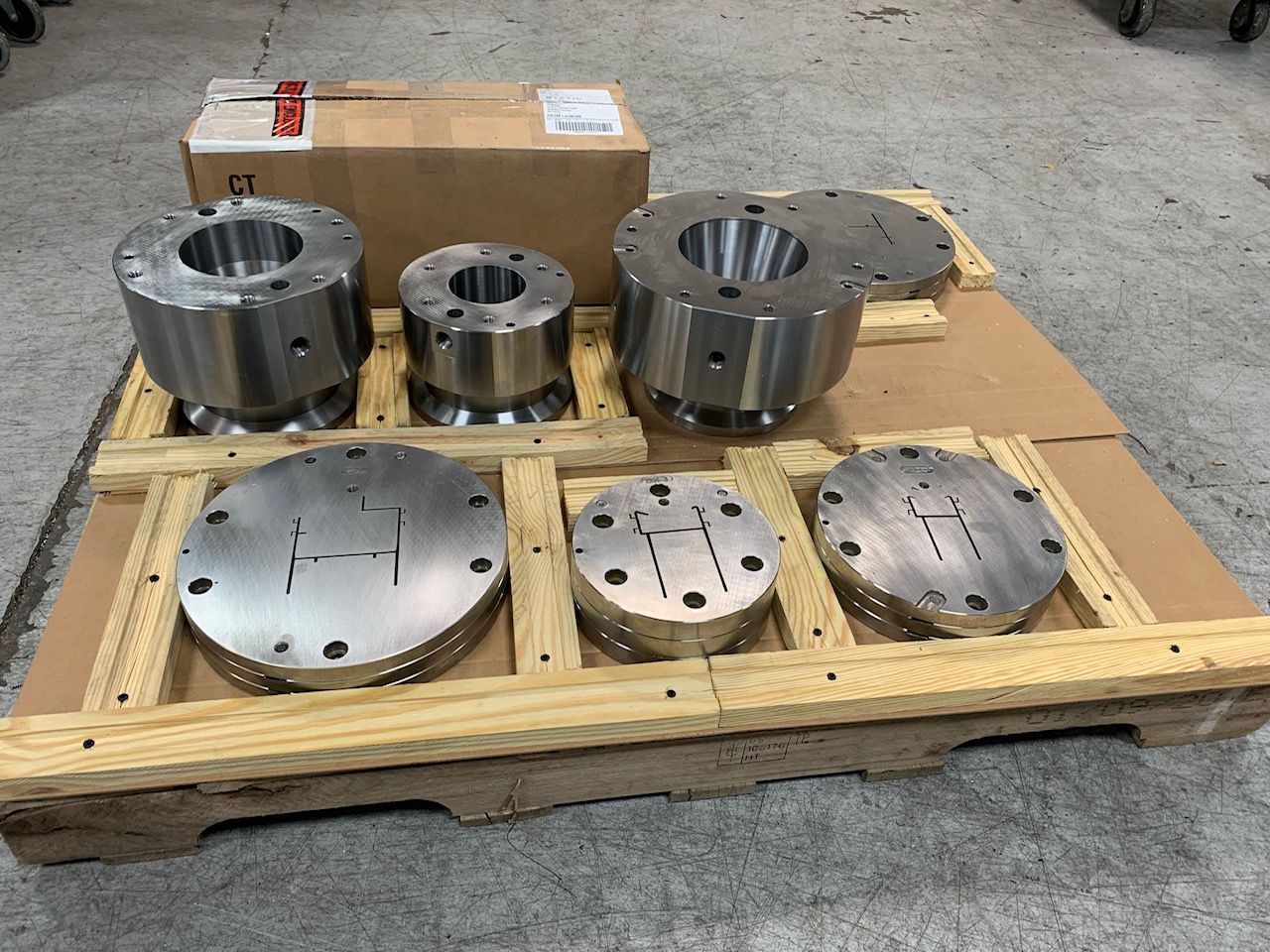
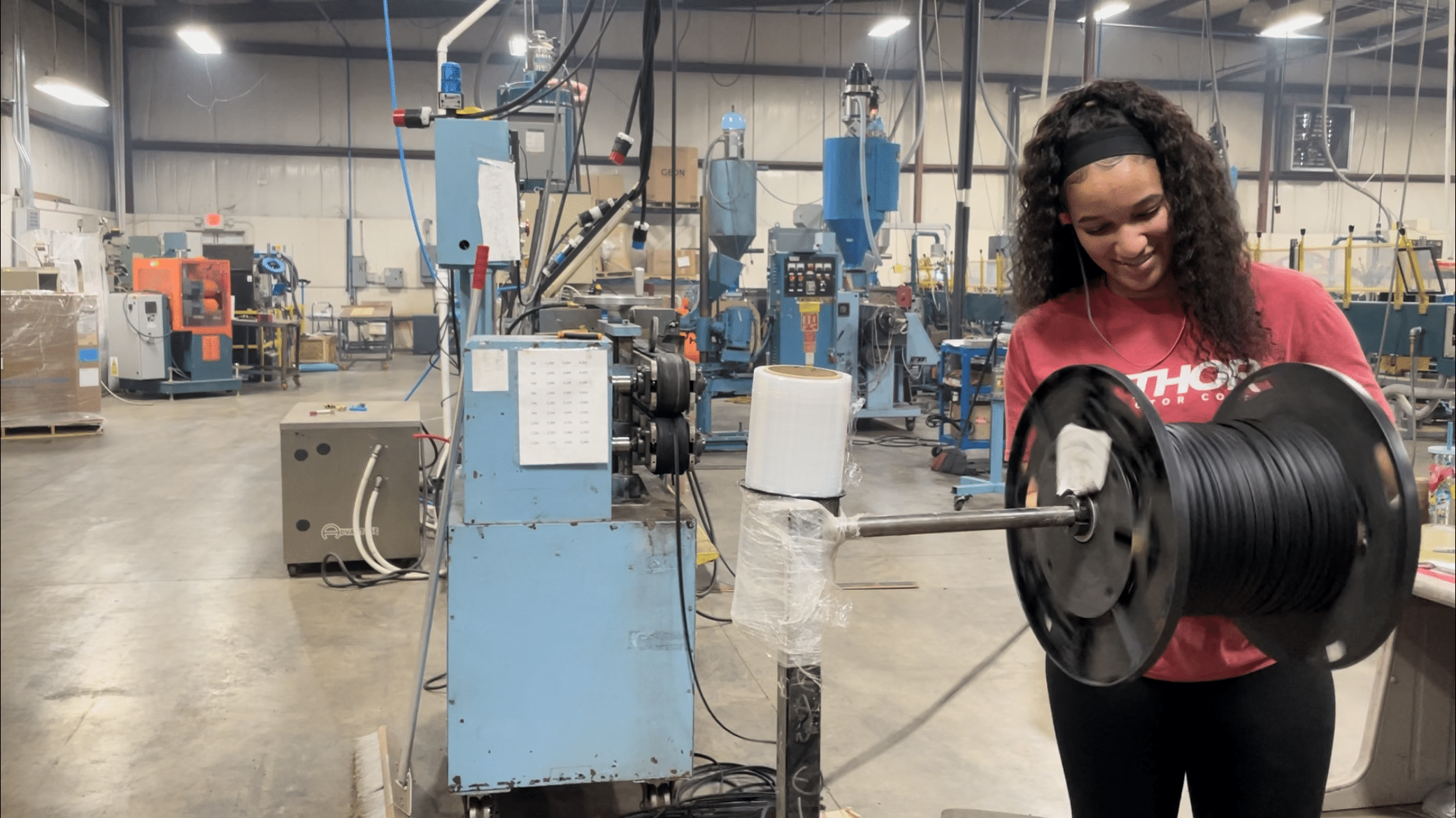